Simulation
From structural analysis and computational fluid dynamics to injection molding simulation and advanced, cloud-enabled capabilities powered by Abaqus, SOLIDWORKS® and 3DEXPERIENCE® Works Simulation provide integrated analysis tools for every designer, engineer, and analyst.
Structural Simulation
Structural Simulation solutions available to SOLIDWORKS users provide a comprehensive set of structural analysis capabilities to guide design decisions and improve product performance and quality.
- CAD-embedded structural analysis solutions using Finite Element Analysis (FEA) to predict real-life performance
- Easy to use, comprehensive capabilities solve everything from a simple linear analysis of single components to complete simulations of full assemblies with contact and non-linearities
- Cloud-enabled solutions deliver access to powerful, proven, and scalable Abaqus technology from SIMULIA
- Understand product performance early in the design process to innovate more and avoid rework
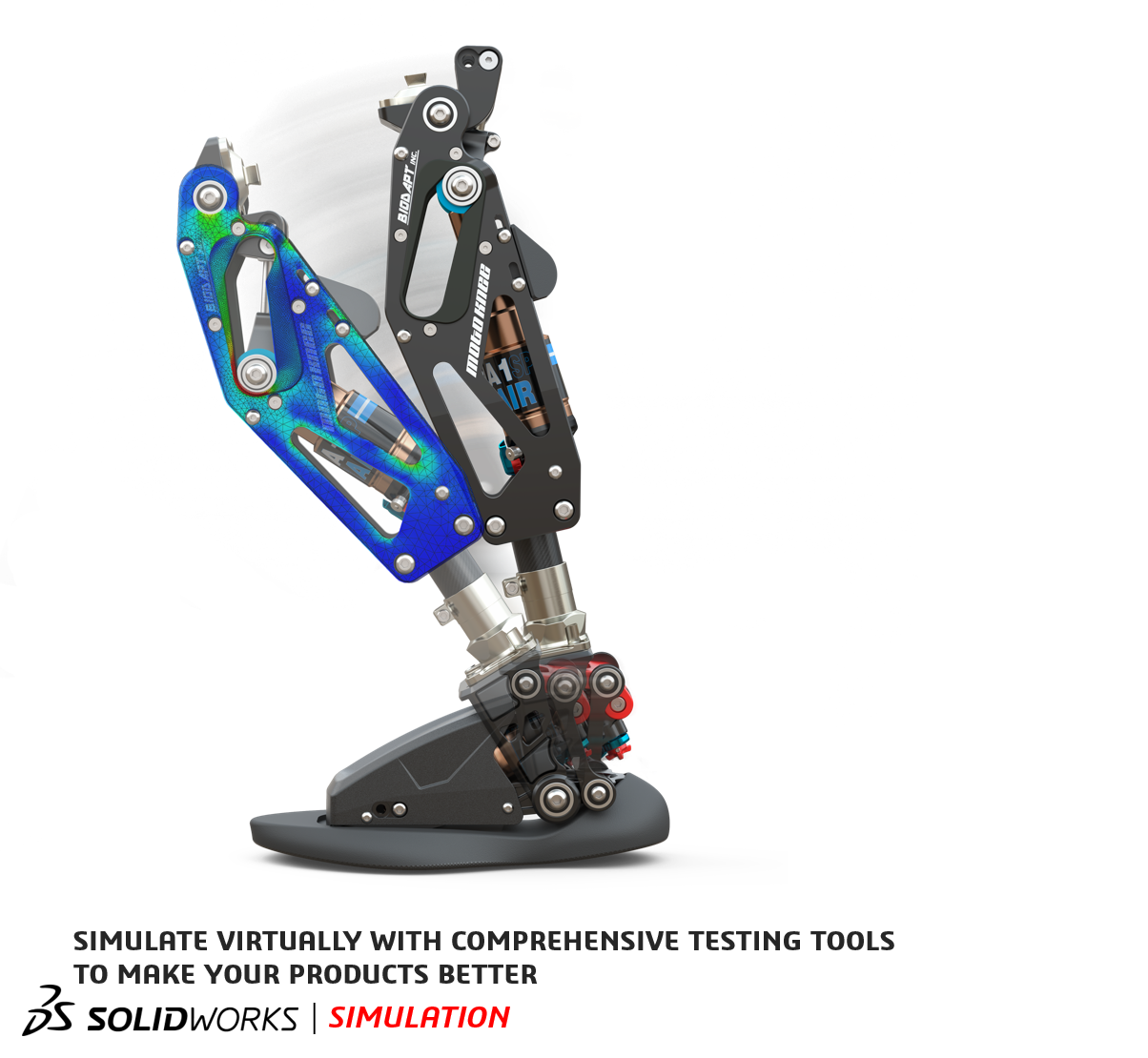
Need more information about our product ?
SOLIDWORKS Simulation Solutions enable you and your team to quickly transform new ideas into great products by simulating and analyzing product behavior.